2010年注冊安全工程師事故案例分析模擬試題(七)
2003年9月5日上午,河南省某運(yùn)輸公司一輛液氨罐車到江西某化肥廠充裝液氨,車主盧某是個(gè)體運(yùn)輸業(yè)主,在該公司,因罐車自帶的液氨充裝軟管與該化肥廠液氨充裝系統(tǒng)接口連接不匹配,就向一旁同在該化肥廠等待灌裝液氨的江西省萍鄉(xiāng)市某廠罐車司機(jī)楊某借用充裝軟管。9時(shí)30分左右,在充裝過程中,裝卸軟管的液相管突然爆裂,大量液氨外泄,瞬間液氨汽化,白霧頓時(shí)向周圍擴(kuò)散。此時(shí),正在一旁工作或等候充裝的人員共有4人:河南罐車司機(jī)、河南罐車車主盧某、該化肥廠液氨亢裝員、萍鄉(xiāng)市某廠罐車司機(jī)楊某。事故發(fā)生后,其中3人迅速跑離現(xiàn)場,河南罐車車主盧某因躲避不及,中毒倒地,后經(jīng)送醫(yī)院搶救無效身亡。
試分析事故原因,并提出經(jīng)驗(yàn)教訓(xùn)。
答案:
事故原因分析:
事故發(fā)生后,由該化肥廠主管部門牽頭,安全、質(zhì)監(jiān)、工會(huì)、公安等部門參加,組成了事故調(diào)查組,聘請了技術(shù)專家,對事故全過程進(jìn)行了調(diào)查分析。
1.事故發(fā)生時(shí)該化肥廠液氨充裝系統(tǒng)沒有超壓,氨球罐安全閥沒有起跳,液氨罐車及裝卸軟管的設(shè)計(jì)壓力為2.16MPa,高于該化肥廠充裝系統(tǒng)的工作壓力,經(jīng)專家認(rèn)定,排除了系統(tǒng)超壓充裝。
2.爆裂的液相軟管斷裂成3節(jié),其外表有破損痕跡,內(nèi)層網(wǎng)狀鋼絲銹蝕嚴(yán)重,橡膠具有老化特征。經(jīng)專家認(rèn)定軟管存在質(zhì)量問題,也是發(fā)生事故的直接因素。萍鄉(xiāng)市某廠有2套液氨裝卸軟管,一套是隨罐車配帶的,另一套是從湖南省某貿(mào)易公司購買的,2套軟管經(jīng)常更換使用。從湖南省購買的這套軟管,既無產(chǎn)品合格證,也沒有制造單位,屬“三無”產(chǎn)品。事故發(fā)生后,調(diào)查組到湖南調(diào)查,發(fā)現(xiàn)這家貿(mào)易公司已經(jīng)關(guān)閉,在工商部門的注冊已經(jīng)注銷,店主不知去向。萍鄉(xiāng)市某廠的2套軟管,其中有一套在2002年11月6日隨罐車一起經(jīng)過有關(guān)法定檢測機(jī)構(gòu)檢測,檢測結(jié)果為液相管合格,氣相管不合格。由于檢測單位沒有在經(jīng)過檢測的軟管管體上注明檢測標(biāo)志,時(shí)間一長,以至無法判定這2套軟管是哪一套經(jīng)過了檢測,哪一套沒有經(jīng)過檢測。但有一點(diǎn)可以肯定,萍鄉(xiāng)市某廠罐車司機(jī)使用的裝卸軟管是不合格的或者是沒有經(jīng)過檢測的軟管,并且還將這種裝卸軟管外借他人使用。
3.按照《液化氣體汽車罐車安全監(jiān)察規(guī)程》第47條規(guī)定,汽車罐車隨車必帶的文件和資料包括:汽車罐車使用證、機(jī)動(dòng)車駕駛執(zhí)照和汽車罐車準(zhǔn)駕證、押運(yùn)員證、準(zhǔn)運(yùn)證、汽車罐車定期檢驗(yàn)報(bào)告復(fù)印件、液面計(jì)指示刻度與容積的對應(yīng)關(guān)系表;在不同溫度下介質(zhì)密度、壓力、體積對照表以及運(yùn)行檢查記錄本和汽車罐車裝卸記錄等。而事故罐車提供不出由質(zhì)量技術(shù)監(jiān)督部門及交通部門頒發(fā)的押運(yùn)員證、汽車罐車準(zhǔn)駕證,使用證參數(shù)與罐車銘牌參數(shù)不符。后經(jīng)查實(shí),事故罐車車主盧某沒有經(jīng)過安全培訓(xùn),罐車沒有登記,“六證”不全,罐車為非法運(yùn)輸罐車,不具有運(yùn)輸液氨資質(zhì)。
4.充裝現(xiàn)場不具備必要的充裝條件,該化肥廠在汽車罐車充裝站沒有配備液氨充裝軟管,沒有計(jì)量裝置,沒有裝備氣體濃度監(jiān)測報(bào)警裝置,沒有安裝氣體泄漏自動(dòng)切斷聯(lián)鎖裝置,安全措施不到位,充裝人員在沒有認(rèn)真審查清楚罐車是否具有充裝資質(zhì)的情況下,就給罐車充裝液氨,工作嚴(yán)重失職。
事故教訓(xùn):
1.安全意識不強(qiáng),自我保護(hù)能力差。根據(jù)規(guī)定要求,從事危險(xiǎn)化學(xué)品作業(yè)人員一定要經(jīng)過安全技術(shù)教育,熟悉其所運(yùn)輸介質(zhì)的物理、化學(xué)性質(zhì)和安全防護(hù)措施,了解裝卸的有關(guān)要求,具備處理事故和異常情況的能力,堅(jiān)持按規(guī)定持證上崗,在各項(xiàng)安全條件都具備的情況下,才能從事危險(xiǎn)化學(xué)品的運(yùn)輸作業(yè)。而事故罐車車主是非法經(jīng)營,由于沒有參加安全知識培訓(xùn)教育,對液氨的化學(xué)性質(zhì)以及液氨對人體的危害性認(rèn)識不足,事故發(fā)生后不能有效地采取相應(yīng)措施保護(hù)自己。
2.危險(xiǎn)化學(xué)品經(jīng)營單位液氨充裝站應(yīng)該按照規(guī)范要求進(jìn)行設(shè)計(jì),要有符合國家標(biāo)準(zhǔn)的生產(chǎn)工藝、設(shè)備或設(shè)施,有健全的安全管理制度,配備合格的安全管理人員和操作人員。通過這起事故可以看到,該化肥廠充裝站存在設(shè)計(jì)施工中的安全隱患,如,充裝站的選址不合理,有效空間小,不利于發(fā)生事故后人員撤離;充裝設(shè)施不規(guī)范,沒有自動(dòng)緊急切斷系統(tǒng),等等。
3.加強(qiáng)危險(xiǎn)化學(xué)品運(yùn)輸管理,對“六證”不全的汽車罐車堅(jiān)決不予充裝。目前不少危險(xiǎn)化學(xué)品生產(chǎn)單位為了能使產(chǎn)品盡快出售,對汽車罐車“六證”檢查不嚴(yán)格,對“六證”不全的運(yùn)輸罐車也進(jìn)行充裝,這樣做是對違規(guī)行為的放縱,非常不利于安全生產(chǎn),同時(shí)也為安全事故埋下了嚴(yán)重隱患。危險(xiǎn)化學(xué)品經(jīng)營單位應(yīng)本著對國家負(fù)責(zé)、對人民生命財(cái)產(chǎn)負(fù)責(zé)、對社會(huì)負(fù)責(zé)、對企業(yè)負(fù)責(zé)的精神,加強(qiáng)危險(xiǎn)化學(xué)品的安全管理,認(rèn)真檢查“六證”,對“六證”不全的罐車堅(jiān)決不允許充裝。各級執(zhí)法機(jī)構(gòu),要加強(qiáng)監(jiān)察執(zhí)法力度,發(fā)現(xiàn)問題要堅(jiān)決糾正。被單位也要加強(qiáng)對車輛的安全管理,尤其是對運(yùn)輸危險(xiǎn)化學(xué)品的這種特殊車輛,更要嚴(yán)加管理。
4.液化氣體充裝軟管爆裂傷人事故是非常典型的事故,事故率較高,應(yīng)當(dāng)引起有關(guān)部門的高度重視。如:2004年7月28日12時(shí)50分,中石化上海某公司聚氨酯事業(yè)部,一輛正在卸液氨的槽車金屬軟管突然爆裂,200多千克液氨外泄,造成48人中毒,其中10人中毒嚴(yán)重住院治療。2004年8月1日23時(shí)50分,福建漳州某合成氨廠,一輛正在裝液氨的槽車金屬軟管突然爆裂,lt液氨泄漏,造成1死39傷,其中5人傷勢嚴(yán)重。2004年9月2日,河北邯鄲武安市某化工公司液氨罐車在另一化工公司廠區(qū)內(nèi)充裝液氨,因車帶液氨軟管爆裂,引發(fā)液氨泄漏,造成4人死亡、19人中毒等等。因此,建議各級安全執(zhí)法機(jī)構(gòu)應(yīng)當(dāng)進(jìn)一步加強(qiáng)壓力管道、尤其是像液化氣體充裝軟管這種類型的壓力管道的安全管理,檢測機(jī)構(gòu)應(yīng)在經(jīng)過檢測合格的軟管管體上標(biāo)注合格標(biāo)志,充裝使用單位在看到這種標(biāo)志后才可使用。
5.企業(yè)領(lǐng)導(dǎo)必須高度重視安全生產(chǎn)工作,牢固樹立“安全第一”的指導(dǎo)思想,把安全生產(chǎn)作為頭等大事來抓,要從事故中吸取教訓(xùn),單一反三。通過這起事故,對全廠各個(gè)崗位進(jìn)行排查,查找事故隱患,發(fā)現(xiàn)后堅(jiān)決整改,確保生產(chǎn)安全穩(wěn)定進(jìn)行。
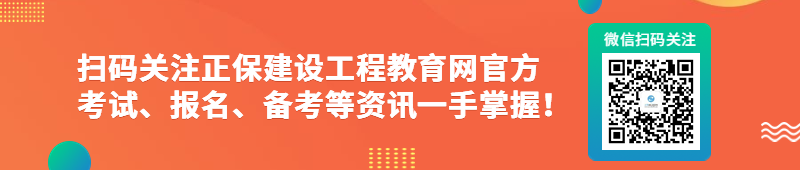

- ·【注意】2017年安全工程師考前模擬題已開通
- ·案例分析安全保障:特種作業(yè)人員的考核發(fā)證
- ·廣西公布2014年安全工程師考務(wù)文件
- ·2013年廣西安全工程師考試報(bào)名時(shí)間為5月15日-6月5日
- ·2012年安全工程師考試沖關(guān)必備
- ·2012年安全工程師:安全生產(chǎn)事故案例分析
- ·2012年《注冊安全工程師》考試復(fù)習(xí)指導(dǎo)全程
- ·2010年安全工程師考試《安全生產(chǎn)管理知識》習(xí)題(一)
- ·2010年安全工程師《安全生產(chǎn)管理知識》精華習(xí)題(76)
- ·2010年安全工程師考試《管理知識》模擬題(57)